8.2.2 Detailed Design Procedure
8.2.2.1 Thermal Performance
Output power is limited by three things: the peak current limit, the ambient temperature, and the maximum power dissipation in the package. If the die temperature of the device is below the absolute maximum rating of 125°C, the maximum output power can be over 6 W. However, any appreciable output current causes the internal power dissipation to increase and therefore increase the die temperature. Any circuit configuration must ensure that the die temperature remains below 125°C taking into account the ambient temperature derating. The thermal scale-back protection (TSB) helps ensure that temperature requirement is held valid. If the TSB feature is disabled, thermal shutdown (TSD) is the next level of protection for the device, which is set to 150°C. This mechanism cannot be disabled, and operation of the device above 125°C is not ensured by the electrical specification.
In boost mode, where VIN < VLED + VHR, the power dissipation can be approximated by Equation 1:
Equation 1. 
When the device is in pass mode, where VIN > VLED + VHR, the power dissipation equals:
Equation 2. 
Use Equation 3 to calculate the junction temperature (TJ) of the device:
Equation 3. 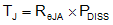
Note that these equations only provide approximation of the junction temperature and do not take into account thermal time constants, which play a large role in determining maximum deliverable output power and flash durations.
8.2.2.2 Output Capacitor Selection
The LM36010 is designed to operate with a 10-µF ceramic output capacitor. When the boost converter is running, the output capacitor supplies the load current during the boost converter on-time. When the NMOS switch turns off, the inductor energy is discharged through the internal PMOS switch, supplying power to the load and restoring charge to the output capacitor. This causes a sag in the output voltage during the on-time and a rise in the output voltage during the off-time. Therefore, choose the output capacitor to limit the output ripple to an acceptable level depending on load current and input or output voltage differentials and also to ensure the converter remains stable.
Larger capacitors such as a 22-µF or capacitors in parallel can be used if lower output voltage ripple is desired. To estimate the output voltage ripple considering the ripple due to capacitor discharge (ΔVQ) and the ripple due to the capacitors ESR (ΔVESR), use Equation 4 and Equation 5:
For continuous conduction mode, the output voltage ripple due to the capacitor discharge is:
Equation 4.
The output voltage ripple due to the output capacitors ESR is found by:
Equation 5. 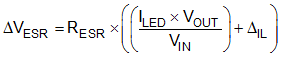
In ceramic capacitors, the ESR is very low so the assumption is that 80% of the output voltage ripple is due to capacitor discharge and 20% from ESR. Table 2 lists different manufacturers for various output capacitors and their case sizes suitable for use with the LM36010.
8.2.2.3 Input Capacitor Selection
Choosing the correct size and type of input capacitor helps minimize the voltage ripple caused by the switching of the boost converter and reduces noise on the input pin of the boost converter that can feed through and disrupt internal analog signals. In the typical application circuit a 10-µF ceramic input capacitor works well. It is important to place the input capacitor as close as possible to the LM36010 input (IN) pin. This reduces the series resistance and inductance that can inject noise into the device due to the input switching currents. Table 2 lists various input capacitors recommended for use with the LM36010.
Table 2. Recommended Input/Output Capacitors (X5R/X7R Dielectric)
MANUFACTURER |
PART NUMBER |
VALUE |
CASE SIZE |
VOLTAGE RATING |
TDK Corporation |
C1608JB0J106M |
10 µF |
0603 (1.6 mm × 0.8 mm × 0.8 mm) |
6.3 V |
TDK Corporation |
C2012JB1A106M |
10 µF |
0805 (2 mm × 1.25 mm × 1.25 mm) |
10 V |
Murata |
GRM188R60J106M |
10 µF |
0603 (1.6 mm × 0.8 mm × 0.8 mm) |
6.3 V |
Murata |
GRM21BR61A106KE19 |
10 µF |
0805 (2 mm × 1.25 mm × 1.25 mm) |
10 V |
8.2.2.4 Inductor Selection
The LM36010 is designed to use a 0.47-µH or 1-µH inductor. Table 3 lists various inductors and their manufacturers that work well with the LM36010. When the device is boosting (VOUT > VIN) the inductor is typically the largest area of efficiency loss in the circuit. Therefore, choosing an inductor with the lowest possible series resistance is important. Additionally, the saturation rating of the inductor must be greater than the maximum operating peak current of the LM36010. This prevents excess efficiency loss that can occur with inductors that operate in saturation. For proper inductor operation and circuit performance, ensure that the inductor saturation and the peak current limit setting of the LM36010 are greater than IPEAK in Equation 6:
Equation 6. 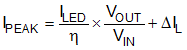
Efficiency details can be found in the Application Curves.
Table 3. Recommended Inductors
MANUFACTURER |
L |
PART NUMBER |
DIMENSIONS (L×W×H) |
ISAT |
RDC |
TOKO |
0.47 µH |
DFE201610P-R470M |
2 mm × 1.6 mm × 1 mm |
4.1 A |
32 mΩ |
TOKO |
1 µH |
DFE201610P-1R0M |
2 mm × 1.6 mm × 1 mm |
3.7 A |
58 mΩ |