11.1 Board Layout
- VINx and VOUTx traces should be as short and wide as possible to accommodate for high current.
- Use vias under the exposed thermal pad for thermal relief for high current operation.
- The VINx terminals should be bypassed to ground with low ESR ceramic bypass capacitors. The typical recommended bypass capacitance is 1-µF ceramic with X5R or X7R dielectric. This capacitor should be placed as close to the device terminals as possible.
- The VOUTx terminals should be bypassed to ground with low ESR ceramic bypass capacitors. The typical recommended bypass capacitance is one-tenth of the VIN bypass capacitor of X5R or X7R dielectric rating. This capacitor should be placed as close to the device terminals as possible.
- The VBIAS terminal should be bypassed to ground with low ESR ceramic bypass capacitors. The typical recommended bypass capacitance is 0.1-µF ceramic with X5R or X7R dielectric.
- The VDD terminal should be bypassed to ground with low ESR ceramic bypass capacitors. The typical recommended bypass capacitance is 0.1-µF ceramic with X5R or X7R dielectric.
- ADDx pins should be tied high to VDD through a pull-up resistor or tied low to GND through a pull-down resistor.
The maximum IC junction temperature should be restricted to 125°C under normal operating conditions. To calculate the maximum allowable power dissipation, PD(max) for a given output current and ambient temperature, use the following equation:
Equation 4.
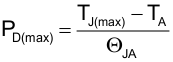
Where:
PD(max) = maximum allowable power dissipation
TJ(max) = maximum allowable junction temperature (125°C for the TPS22994)
TA = ambient temperature of the device
ΘJA = junction to air thermal impedance. See Thermal Information section. This parameter is highly dependent upon board layout.
The figure below shows an example of a layout.